|
Immersion
Heaters |
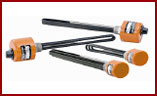 |
Tubular
heating elements are brazed or welded in a brass, steel or stainless
steel pipe plug. Ratings from 350 watts to 38kw and numerous variations
and options are available. Pipe plug immersion heaters are generally
used in small to medium size containers at pressures up to 3000 psi
and are screwed directly through a threaded opening in the tank wall. |
Standard
Products |
|
- 1",
1-1-4", 2" and 2-1/2" NPT pipe plug in brass, steel
or stainless steel
- .312"
diameter tubular element(s) on 1" and 1-1/4"; .475 diameter
elements on 2" and 2-1/2" or .275" x 1" Mighty-Blade
element(s)
- Copper, steel,
stainless steel, or Incoloy sheath material
- High, medium
and low watt densities for various processes
- General purpose
or explosion and moisture resistance terminal enclosures
- Tubular element
send are repressed after forming to extend element life
- Element supports
on larger size units maintain element spacing
- Single and
double pole thermostats in several temperature ranges
- Many items
are available from stock
- Instruction
Manual with wiring diagrams are included with each unit
|
Applications: |
|
Copper
Sheath: |
Clean
water, freeze protection, hot water storage, boiler and water heaters,
cooling towers, heating of solutions not corrosive to copper |
Stainless
Steel Sheath: |
Process
water, soap and detergent solutions, soluble cutting oils, demineralized
or deionized water (passivation recommended) |
Incoloy
Sheath: |
Solution
water, corrosive solutions, steam super heating, air or gas |
Steel
Sheath |
Asphalt,
wax, paraffin, tar, fluid heat transfer medium, petroleum, degreasing
and solvent oils, machine oil, fuel oils, alcohol |
Be
certain that the sheath material and watt density selected are compatible
with the material being heated and the operating temperature.
|
Options: |
Ordering
Information: |
|
- Special ratings,
immersion length, or thread size
- 316 stainless
steel or other sheath material
- Other material
for pipe plug
- Passivation
- Electropolishing
- High temperature
cut-out
- Thermocouple
attached to sheath for high-limit protection
|
- Part Number
- If ordered
with thermostat, specify temperature range
- Other ooptions
- If Part Number
is not available, provide a complete description, sketch or drawing
or contact Hampton Controls Technical
|
|
Over
the Side Heaters |
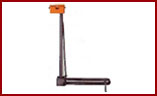 |
Used
in tanks where through-the-wall heaters cannot be installed, portability
is required, or where heaters must be removed for cleaning without
emptying the tank. Suitable for freeze protection, for heating viscous
materials to improve flow, or most open tank applications with proper
sheath and watt density selection. |
- Lightweight
and portable
- Self supporting
- All compatible
materials
- Stainless
steel elements; stainless steel rise and junction box
- Incoloy elements;
stainless steel riser and junction box
- Steel elements;
steel riser and junction box
- Watertight
terminal housing with terminal block for wiring
- Thermowell
for installation of thermostat
- Sludge legs
- .475"
diameter elements
|
Options: |
- Built-in-thermostat:
60-250° F or 150-550° F
- Explosion
resistant terminal enclosure
- Shorter or
longer riser height
- Special ratings
or materials
- Right angle
risers
- Passivation
or other external finishing
- Thermocouple
for process control or high limit
- Mighty-Blade
elements
|
Tubular
Heaters (Formed or Straight) |
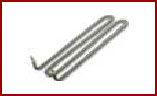 |
The
most versatile of all electric heating elements, the tubular heater
is capable of being formed into virtually and configuration. The basic
design consists of a helical coil of nickel-chromium resistance wire
precisely centered in a metal sheath. THe coil is surrounded by magnesium
oxide powder which is vibration loaded to insure even density throughout
the length of the heater. This entire assembly is then reduced to
the finished diameter, compacting the MgO and "freezing"
the coil in the center of the heater. The range of ratings, sizes,
materials and terminations available makes the tubualr heater adaptable
to many industrial, commercial and scientific applications. |
Sheath
Materials: |
|
Copper
Sheath: |
Water
heating, water solutions non-corrosive to copper |
Stainless
Sheath: |
Immersion
in oils, molten salt baths, alkaline cleaning solutions, tars and
asphalt. Also suitable for clamping to metal surfaces and casting
into aluminum |
|
Stainless
Steel Sheath: |
Corrosive
liquids, food processing equipment |
Incoloy
Sheath: |
Air
heating, radiant heating, cleaning and degreasing solutions, plating
and pickling solutions, corrosive liquids. |
|
Other
sheath materials are also available for application considerations.
Commonly specified are 316 stainless steel, sopper clad steel for
metal casting, Inconel for high temperature applications, and titanium
for severely corrosive solution heating. |
(Back
to Top)
Cast
Heaters (Aluminum, Brass, or Bronze) |
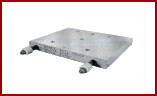 |
Typical
Cast Heater Designs |
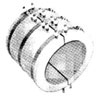 |
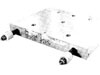 |
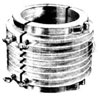 |
Cylindrical
Heat and Cool Heaters for Extrusion Machinery |
Platen
Heaters for Packaging, Food Warning & Die Heating |
Cylindrical
Finned Heaters for Air-Cool Extrusion Machinery |
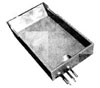 |
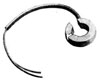 |
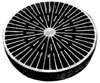 |
Glue
Potts and Pan Heaters for Industrial and Food Warming Applications |
Small
Diameter Cylindrical Heaters for Pipe, Die, and Nozzle Heating |
Special
Cast Heater Designed per exact specifications for your Heating Requirements |
Heater
Specifications: |
|
Other
sheath materials are also available for application considerations.
Commonly specified are 316 stainless steel, sopper clad steel for
metal casting, Inconel for high temperature applications, and titanium
for severely corrosive solution heating. |
Heater
Specifications: |
Cast
Materials |
Max.
Operating Temperature |
Machine
Finish |
|
|
|
Aluminum
Brass
Bronze |
750°
F (400° C)
1200° F (649° C)
1350° F (732° C) |
A
finish of 125 RMS can be provided on any flat and I.D. surfaces
when required. Platen surfaces can be belt sanded to within .005"
or milled to .001" flat. |
Electrical |
Holes,
Cutouts, Thermowells |
|
|
•
Resistance tolerance: NEMA standard + 10% - 5% |
Mounting
or clearances holes, cutouts, and thermowells for inserting temperature
measurement probes can be cast-in or machined per your specifications |
•
Voltages: |
Element
diameter |
.260 |
.315 |
.430 |
|
|
|
|
Maximum
volts |
240 |
277 |
600 |
Inserts |
(Three
Phase available on large heaters) |
|
•
Maximum watt densities depends on size and application. Consult
Factory. |
Threaded
studs, precision coomponent parts, bushings, and special design
parts can be accurately cast in place. |
Ordering
Notes: |
Testing |
1.
Cast design. Supply a complete drawing showing all dimensions and
critical tolerances. |
3.
Electrical terminations and housings |
|
- Electrical
- Dimensional per specifications
- Preccure test of cooling tubes when applicable
|
2.
Heater element and cooling tube (if required) exit locations. |
4.
Wattage and voltage ratings |
5.
Quantity |
(Back
to Top)
Radiant
Heaters |
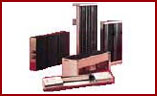 |
With
Hampton Controls diverse radiant heater line, we have a solution
for almost any application requiring radiant heat. Our capabilities
cover a wide range of needs, from contamination-resistant panel
heaters to fast-responding quartz tubes to rugged tubular elements
and high temperature ceramic panels.
Applying radiant heaters can be complicated. Hampton Controls engineering
staff has the level of training required to help you meet your application
requirements, providing a high degree of technical support such
as conducting testing for your application at our facility, calculating
your watt density and temperature requirements, and recommending
system components such as sensors and controllers. With our experience
in a wide range of industries, chances are Hampton Controls has
already helped someone handle a radiant heating application like
yours. |
Sheath
Material |
Typical
Max. Watt Densities |
Max.
Operating Temperatures |
|
W/cm2 |
W/in2 |
|
Incoloy®
Tubular |
6.2 |
40 |
815°
C (1500° F) |
Molded ceramic
fiber |
4.6 |
30 |
1095°
C (2000° F) |
Quartz tube |
7.0 |
45 |
870°
C (1600° F) |
Stainless steel
emitter strip |
4.6 |
30 |
700°
C (1300° F) |
|
|
|
|
Applications |
|
|
|
- Thermoforming
- Food warming
- Paint and
epoxy curing
|
- Heat treating
- High temperature
furnaces
- Tempering
and annealing processes
|
(Back
to Top)
Air
Heaters |
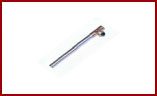 |
Hampton
Controls stocks several variations of 1/2" diameter air heaters
for the heat staking industry. |
Construction |
Specifications |
- Stainless
steel sheath
- Optional
36" fiberglass insulated leads or 3 prong socket
- Epoxy seal
- Copper
Tee
- Optional
brass 1/8" female NPT or 3/8" male NPT fittings on
inlet or outlet.
- Optional
thermocouple
|
- Maximum
amps: 10
- Maximum
CFM: 10
- Use clean
air only
|
The
following heaters are in stock for immediate delivery |
Volts |
Watts |
With
36" leads |
With
3 prong socket |
Min.
CFM |
120 |
400 |
AH50050R |
AH50050S |
4 |
240 |
400 |
AH50050T |
AH50050U |
4 |
120 |
600 |
AH50050V |
AH50050W |
5 1/2 |
240 |
600 |
AH50050X |
AH50050Y |
5 1/2 |
(Back
to Top)
Silicon
Rubber Heaters |
Flexible
Heaters, Silicone Rubber Heaters, Drum Heaters, Kapton Heaters,
Neoprene Heaters |
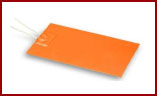 |
Flexible
heaters from Hampton Controls are just what the name implies; thin,
bendable and shaped to fit your equipment. You can use your imagination
to apply heat to the most complex shapes geometries conceivable
without sacraficing efficiency or dependability. |
Sheath
Material |
Typical
Max. Watt Densities |
Suggested
Watt Densities |
Max.
Operating Temperatures |
|
W/cm2 |
W/in2 |
W/cm2 |
W/in2 |
|
Silicone rubber |
12.4 |
80 |
0.78 |
5 |
260°
C (500° F) |
Polymide (Kapton®) |
12.4 |
80 |
0.78 |
5 |
200°
C (390° F) |
HT foil |
17.0 |
110 |
3.1 |
20 |
595°
C (1100° F) |
Neoprene |
1.7 |
11 |
0.31 |
2 |
120°
C (250° F) |
|
|
|
|
Applications |
|
|
|
- Medical
equipment such as blood analyzers, respritory therapy units
and hydrotherapy baths
- Freeze
protection for military hardware, aircraft instrumentation and
hydraulic equuipment
|
- Battery
heating
- Foodservice
equipment
- Factory
bonding and subassemblies
- Any application
requiring a flexible shape or design
|
(Back
to Top)
Ceramic
Heaters |
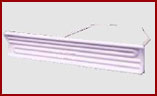 |
Ceramic
fiber heaters intergrate a high temperature iron-chrome-aluminum
(ICA) heating element wire with ceramic fiber insulation. Numerous
stock, standard and/or custom shapes can be provided, acheiving
the "heated insulation" concept for your high temperature,
non-contact applications. The ceramic fiber insulation isolates
the high temperatures inside the heated chamber from the outside.
The heaters are low meass, fast heating, with high insulation values
and slef-supported heating elements that offer some of the highest
temperature heating capabilities within the Hampton family of heater
designs. |
Sheath
Material |
Typical
Max. Watt Densities |
Max.
Operating Temperatures |
|
W/cm2 |
W/in2 |
|
Molded
ceramic fiber |
1.8 |
11.5 |
1205°
C (up to 2200° F) |
|
|
|
|
Applications |
|
|
|
- High temperature
furnaces
- Metal melting,
holding and transfer
- Semiconductor
processing
- Glass,
ceramic and wire processing
|
- Analytical
instrumentation
- Fluisized
beds
- Laboratory
and R&D
- Other high
temperature process applications
|
(Back
to Top)
|